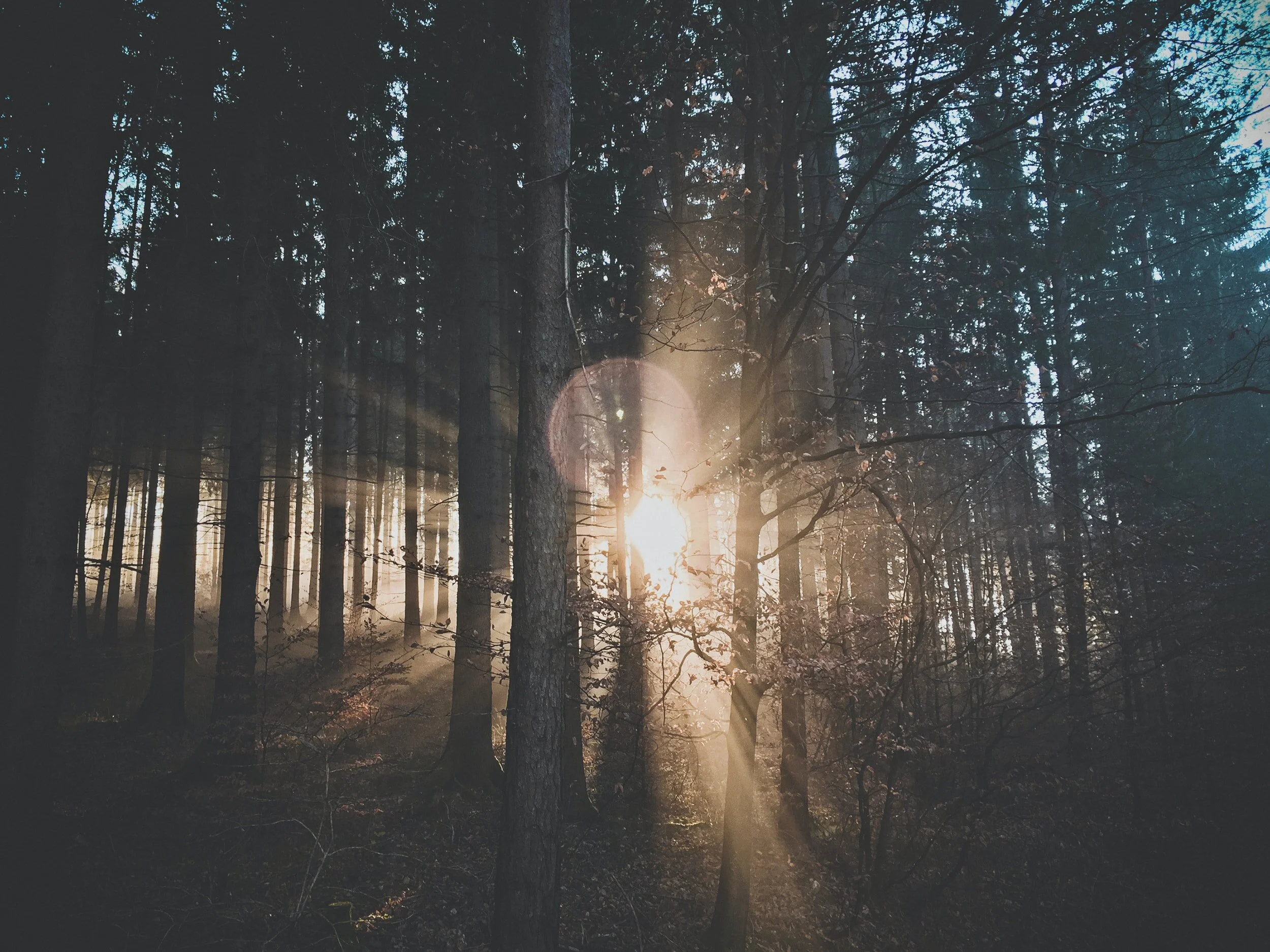
The Energy Efficiency of
Log Homes
The logs release this heat into the home, providing warmth in the night. The net effect of the log’s thermal mass is to decrease the heat gain in the day and lessen the heat loss at night, moderating the room temperature and providing benefits beyond what is captured by a simple R-value measurement.
R-Value vs. Thermal Mass
‘R’ – value measures a material’s resistance to the transfer of heat from one side to another. Logs have a relatively low resistance to heat transfer as they actually absorb and store heat in their cellular structure. Thus taking a longer period of time to transfer through the material.
Thermal Mass is a material’s capacity to absorb, store and slowly release heat over time.
The R-Value of Wood
A material’s thermal resistance or resistance to heat flow is measured by its R-value. In a solid log wall, the logs provide both structure and insulation. The R-value for wood ranges between 1.41 per inch (2.54 cm) for most softwoods and 0.71 for most hardwoods. Ignoring the benefits of the thermal mass, a 6-inch (15.24 cm) softwood log wall has a clear-wall (a wall without windows or doors) R-value of just over 8.
Compared to a conventional wood stud wall (3½ inches (8.89 cm) of insulation, sheathing, and wallboard, for a total of about R-14) the log wall is apparently a far inferior insulation system. Based only on this, log walls do not satisfy most building code energy standards. However, to what extent a log building interacts with its surroundings depends greatly on the climate. Because of the log's heat storage capability, its large mass may result in better overall energy efficiency in some climates than in others.
Logs act like "thermal batteries" and can, under the right circumstances, store heat during the day and gradually release it at night. This generally increases the apparent R-value of a log by 0.1 per inch of thickness in mild, sunny climates that have a substantial temperature swing from day to night. Such climates generally exist in the Earth's temperate zones between the 15th and 40th parallels.
Minimizing Air Leakage
Log homes are susceptible to developing air leaks. Air-dried logs are still about 15%–20% water when the house is assembled or constructed. As the logs dry over the next few years, the logs shrink. The contraction and expansion of the logs open gaps between the logs, creating air leaks, which cause drafts and increase high heating and cooling requirements.
To minimize air leakage, logs should be seasoned (dried in a protected space) for at least six months before construction begins.
Because most manufacturers and experienced builders know of these shrinkage and resulting air leakage problems, many will kiln dry the logs prior to finish shaping and installation. Some also recommend using plastic gaskets and caulking compounds to seal gaps. These seals require regular inspection and resealing as necessary.
Controlling Moisture
Because trees absorb large amounts of water as they grow, the tree cells are also able to absorb water very readily after the wood has dried. For this reason, a log home is very hydroscopic -- it can absorb water quickly, which can promote wood rot and insect infestation.
It is strongly recommended that you protect the logs from contact with any water or moisture. One moisture control method is to use only waterproofed and insecticide-treated logs, and reapply these treatments every few years for the life of the house. Generous roof overhangs, properly sized gutters and downspouts, and drainage plains around the house are also critical for moisture control.
Building Energy Code Compliance
Because log homes don't have conventional wood-stud walls and insulation, they often don't satisfy building code energy standards that require prescribed insulation R-values. However, several states -- including Pennsylvania, Maine, and South Carolina -- have exempted log-walled homes from normal energy compliance regulations. Others, such as Washington, have approved "prescriptive packages" for various sizes of logs, but these may or may not make sense in terms of energy efficiency.
The American Society of Heating, Refrigerating, and Air Conditioning Engineers (ASHRAE) 90.2 standard contains a thermal mass provision that may make it easier to get approval in states that base their codes on this standard. To find out the log building code standards for your area, contact your city or county building code officials. Your state energy office may be able to provide information on energy codes recommended or enforced in your state.
For designing an energy-efficient log home, you should consider using the whole-house systems approach and incorporating some passive solar design features.
Pickett, R., ed. (2003). The Energy Performance of Log Homes, Log Homes Council, National Association of Home Builders.
Roos, C.; Eklund, K.; Baylon, D. (1993). The Thermal Performance and Air Leakage Characteristics of Six Log Homes in Idaho; RCD
Thermal Mass Benefits of
Log Homes Recognized
The situation could be cause for adopting an “I told you so” attitude, but that won’t happen. “The Log Homes Council (LHC) doesn’t feel smug, it just feels vindicated,” says Barbara Martin, LHC’s executive director.
The situation in question is the fact the nation’s Model Energy Code finally recognizes the energy- conservation benefits of thermal mass. This is a victory for the LHC. After 13 years, its claim, a log wall’s thermal mass makes it as energy efficient as a well-insulated frame wall, has been acknowledged. Achieving this acceptance has been a major goal for the LHC, a part of the Building System Councils of the National Association of Home Builders (NAHB).
While the claim is true, it wasn’t officially acknowledged, in part because thermal mass is difficult to quantify. Log homeowners had the home heating bills to prove it was true, but Department of Energy and code officials needed more than empirical evidence. So, over the past 13 years, the LCH has gathered scientific statistics from independent research projects to substantiate its assertion.
Now that it has succeeded, Dave Carter, LHC energy committee chairman, says “This makes life easier for log home producers. We no longer have to fight energy codes based on R-values. It also helps log homes owners. They don’t have to invest in additional building materials to meet codes that do not improve the livability of their homes.”
R-values measure a material’s resistance to the transfer of the heat from one side to another. Logs have a relatively low resistance to heat transfer. In fact, they actually absorb and store heat in their cellular structure. This puts logs at a serious disadvantage in the cold winter states. It forced producers to overbuild their homes, especially their floor, window and roof systems, to meet total R-value requirements. “This drove up construction costs without any measurable benefit to our buyers,” says Carter.
R-values have been at the heat of the debate all along. When the energy crisis struck in the 1970’s, the state and federal governments quickly developed new energy standards for residential construction. To assure compliance, officials needed a way to assure the energy performance of all residential building material. Since the situation was a crisis, and the R-value methodology existed, it became the standard.
Thermal mass is a material’s capacity to absorb, store and slowly release heat over time. Logs do this well. The LHC set out to prove two things. First, logs have thermal mass because of their cellular structure, bulk and thickness. Second, this thermal mass provides significant energy saving benefits because it releases heat back into the house when temperatures drop.
Early studies proved thermal mass properties significantly reduce heating and cooling loads in moderate climates. The National Institute of Standards conducted the most important of these studies for HUD in 1981-82. However, energy experts continued to question the value of thermal mass during the winter months in northern climates. They doubted its benefit when heat is needed constantly and thermostat settings are opposite outdoor temperature.
Two recent studies, both conducted in cold climate states, answer this question to the log home industry’s benefit. In 1990, an independent testing agency, Advanced Certified Thermograghy, conducted a study for the Energy Division of the Minnesota Department of Public Service. It focused on heat loss through air leakage, assumed to be a problem with log walls because of their many joints. The study found the industry has substantially reduced air infiltration rates in the past 15 years. It credited this reduction to improve joint construction and the use of expanded foam sealants and gaskets on all joints and corner intersections. Leakage in the 23 test homes occurred in the same places it does in frame houses: at the peak of the cathedral ceilings, around window and doorframes and along the tops of walls. The study concludes air leakage in well-built, modern log homes is not due to their log walls.
NAHB’s Research Center conducted the second study for the LHC in 1991. It showed the thermal mass of log walls does significantly reduce energy use for heating in cold climates. It based its conclusion on a comparison of the actual energy use of eight log homes to the actual energy uses of eight well-insulated frame houses during one winter. The number of houses was evenly divided between upstate New York and Montana. The study also compared the houses actual energy use to their predicted energy consumption. The results led to the conclusion that log home were as energy-efficient as the frame houses.
“What is significant here is the log walls’ average R-values was 44 percent lower than the frame walls’ average R-value.” says Carter. “Clearly, we must conclude the thermal mass performance of log walls is an advantage to log home owners.”
More than 50 of the nation’s leading log home producers belong to the LHC. It works to improve industry standards, increase awareness of log construction as a method for building attractive homes and overcome obstacles to log home ownership.